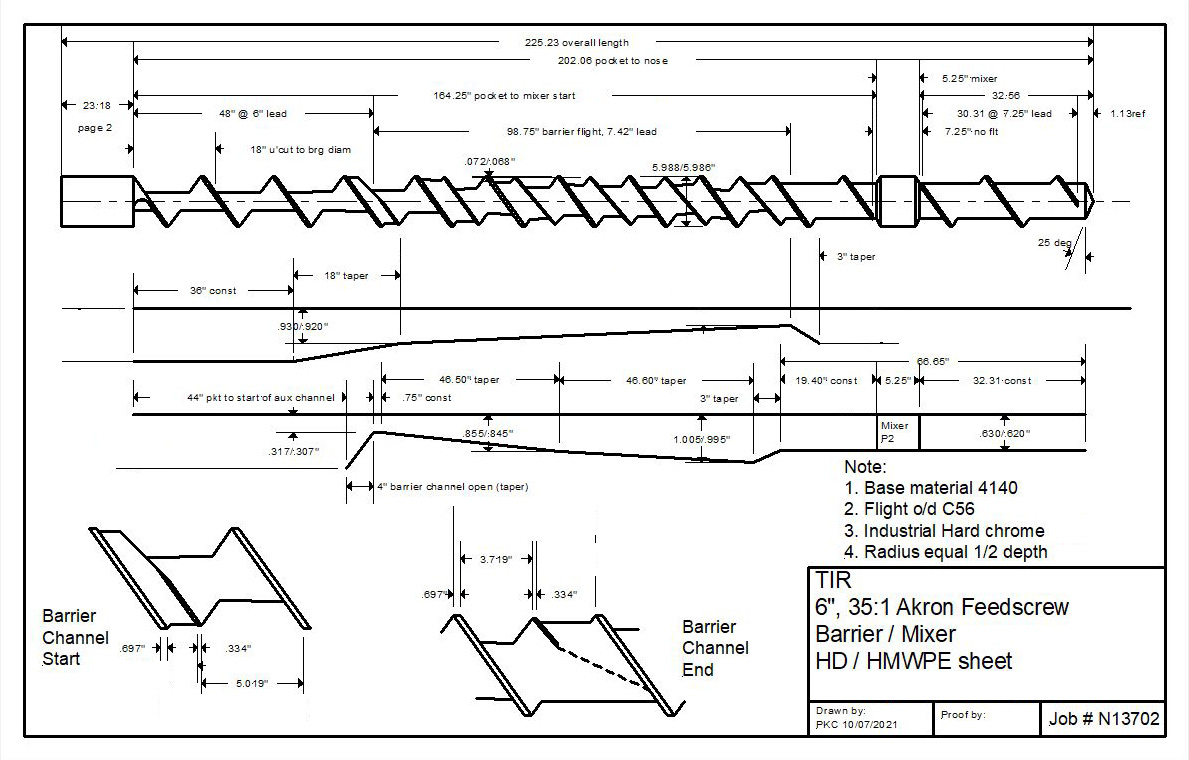
Whatever your application, whatever your process, partner with TIR for meeting your production needs. Feed-Screw Design is a process that begins with our engineering experts working with you to design the new feed-screw, barrel or component that meets your exact requirements.
Our Feed-screw design resource is extremely valuable to your business. With years of experience and specific manufacturing knowledge our feedscrew designers can provide recommendations that improve efficiency and performance ultimately leading to higher performance metrics and better productivity yields.
TIR understands that each manufacturer has unique needs that should be considered when deigning new Feed Screws. OEM designs will universally perform well, but your unique circumstances can provide opportunities for further adjustments and improvements.
When screws or barrels become excessively worn or even damaged there is an opportunity to use a new replacement Feed-screw that meets or exceeds OEM design specifications. Whatever your Feed-screw needs, whether you'd like to stick with your initial OEM design or work with our engineering team and make some adjustments to increase productivity, TIR will partner with you on designing and manufacturing the proper feed screw for your needs.
Let's work together and design the best feedscrew for your line. TIR feedscrews are made in the USA and can be designed to optimize your extrusion or injection molding process. From blown film to sheet extrusion, we can design and manufacture your team a custom feedscrew that will result in greater productivity.
Is your product giving you fits? Bad color mix? Burning? Orange peel? Surging? Let our experienced engineering team design your team a screw that meets your demand for high performance and long wearing screws.
TIR offers complete design & engineering services for single screws, general purpose, resin specific, high performance, wear resistant, and corrosion resistant screws.
Our manufacturing success begins with our engineering experts working with you to design a feedscrew, barrel or component that meets your exact requirements.
Correctly engineered flight profiles on your injection molding screw or extruder screw optimizes processing, and reduces the effects of wear on your screw and barrel components. We are frequently researching materials that would best fit your needs in providing high wear resistance against abrasive, corrosive and adhesive wear. Performance optimization improves processing and will extend the life of not only the screw but the barrel as well. Improved output, better mixing, and critical melt quality can all be achieved through proper screw design. Crystalline and amorphous material process differently so the designs are different for each. Different screw designs and various mixers are available with us at TIR and are selected to achieve desired outcomes. TIR engineers work with our customers to provide the best possible design based on provided requirements.
A feedscrew company that offers feedscrew design services is a valuable resource. With years of experience and specific manufacturing knowledge, a feedscrew designer is able to provide recommendations that improve efficiency and performance using industry experience. OEM designs universally perform well, but a manufacturer usually has unique needs that can be handled with relatively minor adjustments. When production suffers and screws or barrels become excessively worn or even damaged there is an opportunity to use a new replacement part that is better than OEM design specifications.
“Why can’t there be one screw design to run all polymers?” to many people “plastics” are all the same. But, in fact, different plastic types can have very different processing properties. A single screw performs three basic functions: solids conveying, melting and metering or pumping. Each of these functions is controlled by the individual properties of the specific polymer, namely their thermal, viscoelastic, solid and melt density, and frictional properties. These properties can be so diverse that it’s highly unlikely that a universal screw would be able to process them all efficiently. That’s not to say that some polymers cannot be processed at all on a particular screw, but not at their optimum efficiency. (ref. www.ptonline.com Why Are There No `Universal' Screws for All Polymers? Written by Jim Frankland)
Properly engineered flight profiles on your extruder screw or injection molding screw not only optimizes processing, but can reduce the effects of wear on screw/barrel components. We are continually researching new screw and barrel materials that would best fit our customer’s needs in providing high wear resistance against abrasive, corrosive and adhesive wear. Optimizing performance improves processing and will extend the life of the screw and the barrel. Improved output, better mixing, and critical melt quality can all be achieved through proper screw design. Crystaline and amorphous material process differently so the designs are different for each. Different barrier screw designs and various mixers are available from TIR and are selected to achieve desired outcomes. TIR engineers work with our customers to provide the best possible design based on customer requirements, including documented inspections, complete upsize, downsize and thermoset conversions.
TIR has had capabilities for rebuilding stainless steel, 4140-HT, 4340-HT, CPM-9V, CPM-10v, Nitrided Nitralloy, and Inconel since 1995.
TIR manufactures and rebuilds a multitude of both simple and very complex mixing sections for injection molding feed screws and extruder screws, selected for your material and application. Please contact us for analysis and advice on mixing section materials and design for your application.
The Case for Performance Driven Feed Screw Design: A single screw preforms three basic functions: solids conveying, melting and metering or pumping. Each of these functions is controlled by the individual properties of the specific polymer, namely their thermal, viscoelastic, solid and melt density, and frictional properties. These properties can be so diverse that it’s highly unlikely that a universal screw would be able to process them all efficiently. That’s not to say that some polymers cannot be processed at all on a particular screw, but not at their optimum efficiency. For example, let’s compare HDPE with HIPS—two of the more commonly used polymers in extrusion—by looking at their specific heats and processing temperatures, which is the amount of energy (hp) required to bring them to their processing temperature. In this case the processing temperatures of HDPE and HIPS are relatively similar. But HDPE has an average specific heat of 0.55 Btu/lb-°F, while HIPS has an average specific heat of 0.40 Btu/lb-°F. That means it will take 37.5% more hp to raise the temperature of a pound of HDPE to its processing temperature compared with HIPS. Polymer properties can be so diverse that it’s highly unlikely that a universal screw would be able to process them all efficiently. Moreover, HDPE is a crystalline material, meaning it has a defined melting point, while PS is amorphous with no precise melting point. Overcoming HDPE’s crystallinity requires an additional 100 Btu/lb (heat of fusion). So cumulatively, HDPE requires almost 50% more power to reach its processing temperature. Polymers are also defined by their viscoelastic properties, or how the viscosity changes with changing temperature and shear rate. This is a critical property as it determines how much the shear introduced by the rotation of the screw increases the energy entering the polymer. The power-law coefficient (n) is a measure primarily related to the viscosity as affected by shear rate, and the consistency index (m) is a measure related to the viscosity as affected by temperature. These two properties define the changes in melt viscosity with increasing shear rate and temperature. HIPS has about 50% greater change in viscosity with shear than HDPE (see accompanying table). HDPE has about 90% of the solid density of polystyrene but only 77% of the melt density. Basically, HDPE breaks down its ordered structure of crystallinity and expands as the melting occurs. This results in a decrease in output (pounds) through the screw; to get equal output/revolution, the screw channels would have to be 38% deeper for HDPE than HIPS. It also requires compensation in the screw compression rate and volume to accommodate the expansion. As noted above, HIPS has a greater viscosity response to shear rate (power-law coefficient) than HDPE. Therefore, the deeper channels for HDPE to match the lb/hr output of HIPS would result in poor or incomplete melting of HIPS if it were run in the same screw, due to the greater reduction in viscosity and the consequently lower shear melting of the residual HIPS solids. The feeding rate, which governs the total output of the screw, varies with the physical properties of the feed material such as the particle shape, density, bulk density, internal (particle-to-particle) friction and external friction of polymer particles to the metal surfaces of the extruder hopper, feed throat and barrel. Studies have shown PS has a 50% greater dynamic coefficient of friction against steel than does HDPE. This affects its feed rate as well as the degree of compaction of solids in the early screw channels and ultimately its efficiency of melting. Dealing with these differences in polymer properties in the screw design is further complicated by the fact that one difference can offset another. For example, HDPE and PS are certainly not wildly different in the respective properties they provide, yet it’s easy to see why it would be difficult to design one screw that can handle both polymers effectively. Now imagine having to design a screw that can also accommodate higher-melting-point polymers such as PC (see table) or polymers that are typically dried before processing. In these cases, there are some vast differences in properties to deal with. Each property variation can affect the important requirements for efficient and cost-effective processing. The table shows the same properties for PC just to indicate how very different the values are. Consequently, I think we will continue to need specific screw designs for specific polymers. It’s important to point out that once a good design is developed for a particular polymer using all this polymer property data, it does not have to be done afresh for each size of the new screw design. Scale-up/down ratios are used to develop other sizes with good results. Except for very large changes in size that is usually sufficient to produce the necessary performance. (ref. www.ptonline.com Why Are There No `Universal' Screws for All Polymers? Written by Jim Frankland)
The type of material you are processing and your desired production rate are key performance considerations. Be it adjusting material flow rates, controlling mixes, or temperatures we have the experience and knowledge to make effective and competitive recommendations. If you can define what you need to achieve we can design and manufacture a new feedscrew that meets the requirements. In designing a new feedscrew or barrel you have the opportunity to select the feedscrew steel and finishes that will provide optimal wear and longevity. Our feedscrew design experts can discuss material and finish options and decide which of the advantages offered by each your team would like to utilize.
Feed screw design must focus on mixing, pumping, melting and conveying tasks. Application specific elements that affect output include:
Almost all processes using a single screw require some degree of mixing, whether it’s just to homogenize regrind with virgin resin or to mix in some color concentrate. Although there have been many presentations on mixing by experts over the years, processors often find it complicated to apply this information to their own requirements. Many processors also confuse poor melting with poor mixing. Most polymers and additives cannot be effectively mixed until everything that can be melted is melted. As a result, melting and mixing often must be dealt with in the same screw design, although the solutions are often not the same. (ref. www.ptonline.com; Single-Screw Mixing Written by Jim Frankland)
There are three kinds of mixing: dispersive, distributive, and extensional.
4140-HT, 4340-HT, Stainless Steel, Trided Steels, D-2, H-13, CPM 9V, CPMT 420V
Industrial hard chrome, Armoloy, X-1000
Colmonoy 56, 57, 83 & 88, Stellite 6 & 12, Metallurgical N45 & N50
PTA- Plasma Transfer Arc Welding Method and CNC Machining
Give us a call at 1-800-922-7735 and we can work with you on solutions that will meet your needs. TIR can design, rebuild and manufacture a feedscrew from 19mm to 20in diameter and up to 40' in length specific to your process and manufacturing goals.