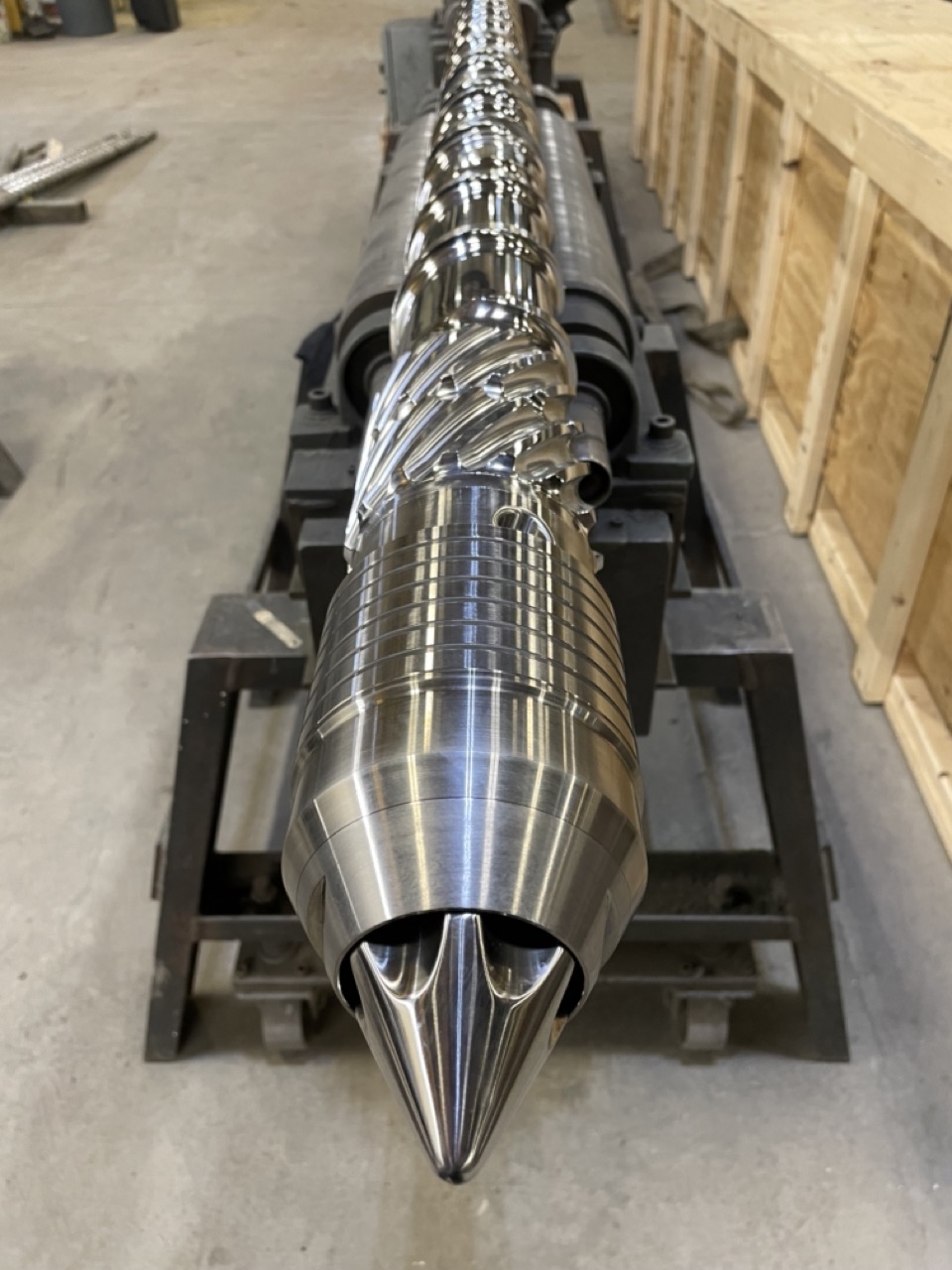
Valves control the flow of the polymer from the extruder to the die that can be used to optimize the output from each stage.
While the least expensive of all the injection molding processing components, a properly designed and built check valve is crucial to good processing.
Many molders treat the check ring (non-return valve) as a simple replacement part - unless major problems arise. Ideally, an injection molding non-return valve’s function is to close after the screw plasticizes a selected amount of resin (shot size) so that this plasticized resin can be forced (injected) into the mold. There are a wide range of cheap general purpose screw tips available on the market, whether OEM or aftermarket. These popular ball check and "free flow" 3 piece and 4 piece ring check valves all have issues that should be taken into account when choosing the right equipment for your molding operation. With thousands of dollars spent on automation, training, machinery, etc. it is important to not overlook some of the most commonly replaced components, the screw and non-return valve. Relying on general purpose, off-the-shelf designs is an expensive policy to undertake.
Non-return valve design originated with the ball check (Fig.1) this valve type has been, and is still used in many Newtonian fluids and applications. Closure in this valve design is accomplished by reverse flow during injection. This is created by forward movement of the screw and valve that moves the ball into a seat that is large enough to accept the recovery flow, but small enough to not allow the ball to pass through. This design seals by contact of the ball OD with the receiving surface of the retaining seat. As there is minimal contact surface, any loss of contact due to misalignment or contamination results in leakage. With Newtonian fluids this is less of a problem than with Non-Newtonian fluids with low viscosities and high elasticity. Example 1b describes the flow that occurs with a minimal opening of 0.002" in an annulus orifice similar to a ball check seal area.
With this example at a hold pressure of 1033 psi (10:1 inject cylinder to barrel id ratio) leakage of 22.25 pph (0.098 oz/sec) is established. The intent of this example is to show that very small clearances due to incomplete sealing can cause significant cushion penetration.
Proper flow paths through valves are important as any "dead spots" that allow for material hang-up can cause degradation and color streaking. In ball check valves, due to the necessary configuration, it is difficult to eliminate "dead spots".
The second type of screw tip that is widely used in the Injection molding industry is the ring check valve. There are two main construction types, 3-piece and 4-piece. The key difference in the construction is that the 4-piece variant allows for a replaceable downstream retainer.
In these traditional free flow valves, closure is accomplished primarily by a minimal clearance from the ring OD to the barrel ID. This tight fit creates friction that attempts to hold the ring in place while the feedscrew rotates, and is forced rearward as the feedscrew develops the necessary pressure to overcome the backpressure resistance. Wear is created by friction on the upstream side of the retainer and the downstream side of the ring, as well as the barrel ID and the ring OD.
Another popular variant of the ring type valve incorporates an interlocking between the upstream side of the retainer and the downstream side of the ring (castellated valve). This design eliminates frictional wear on the retainer as the ring must rotate with the screw. These interlocking designs are more prone to breakage and as the ring is required to rotate with the screw, barrel wear is increased - as the minimum ring to barrel clearance is still required to close the valve.
As the injection barrel wears, traditional free flow loses the friction required for sealing and becomes erratic. This is seen in increased cushion variation, naturally leading to part weight variation. To help stabilize cushion variation more and more decompression (pullback) is used. This helps due to areas of less wear as the valve is moved rearward in the barrel.
Velocity is also important to the closure of traditional ring valves and ball check valves. The greater the velocity the greater the initial sealing force. At slow velocities the separating force created by the resin leaking upstream and the increasing pressure on the upstream side of the ring can be great enough to resist complete closure and cause cushion variation or non-closure.
As we observe the machine requirements to close these valves, it seems that the injection unit is being utilized more to close the valve than its intended purpose of filling the mold.
Decompression was intended to prevent mold drool. Traditional ring valves require decompression or pullback to close consistently. Greater and greater distances are required as the barrel wears to maintain the normal ring to barrel clearance. In many cases splay is created in the molded part due to excessive pullback. Decompression also assists closure in new barrel and valve situations. This is due to the rearward movement of the screw creating a negative pressure by attempting to pull the resin downstream of the feedscrew. As the screw flights create a helical component to the resin flow path, the decompression is greatest at the area from the end of the flight to the ring. This decompression, or reduced pressure, creates less resistance to closure as the screw moves forward due to reduced pressure on the upstream side of the ring.
Ring valves (3 or 4 piece) cannot reduce the distance to close without increasing recovery time and increasing melt temperature. This is due to the increased resistance or pressure drop. Ring valves must have a sealing surface that is not point-to-point contact to minimize leakage during injection. The ring and rear retainer must be properly aligned to seal and the ring thickness must be adequate to resist the inject pressure. If attempts are made to reduce the ring thickness the "hoop strength" can be exceeded causing ring breakage. The thickness and the clearance from ring ID to body OD are the lengths in the pressure drop equation (Fig.2).
Traditional rear seat closing screw tips are prone to leakage and excessive wear on equipment which naturally leads to cushion variation, part weight variation, and unnecessary maintenance costs. The APV (pat. 6203311 & 6464488) was created to have a self cleaning screw tip design that provides shot-to-shot repeatability and accuracy, regardless of initial velocity, without excessive barrel wear.
The screw tip shouldn't be treated as "just a replacement component." The feedscrew and non-return valve are responsible for both quality and efficiency as well as the repeatability of your process. Each APV is designed to be optimized for the material(s) being processed. Compared to traditional "free flow" OEM style screw tips, the APV typically has 1/4 the distance to closure. This means that you will have fast, consistent closure with no leakage.
One of the common, everyday obstacles to achieving the desired part-to-part consistency is the behavior of the typical existing non-return valves - ring and ball-type screw tips. As any molder can testify, these screw tips do not always close immediately at the start of injection - or even close at all on some shots.
Check ring and ball valves are closed by the action of melt flow through the valve. That is, when the forward movement of the screw is initiated to start injection, some backflow of melt through the valve occurs, causing a pressure drop on the upstream side of the sliding or floating member. This causes the valve to close, assuming that the seats are aligned and clear of foreign matter and that screw tip wear does not cause leakage through sealing surfaces. Screw pull back is frequently used to provide ample opportunity for the valve to close. However, the repeater valve is able to close without either any melt flow through the valve or feedscrew movement.
The rich text element allows you to create and format headings, paragraphs, blockquotes, images, and video all in one place instead of having to add and format them individually. Just double-click and easily create content.
A rich text element can be used with static or dynamic content. For static content, just drop it into any page and begin editing. For dynamic content, add a rich text field to any collection and then connect a rich text element to that field in the settings panel. Voila!
Headings, paragraphs, blockquotes, figures, images, and figure captions can all be styled after a class is added to the rich text element using the "When inside of" nested selector system.