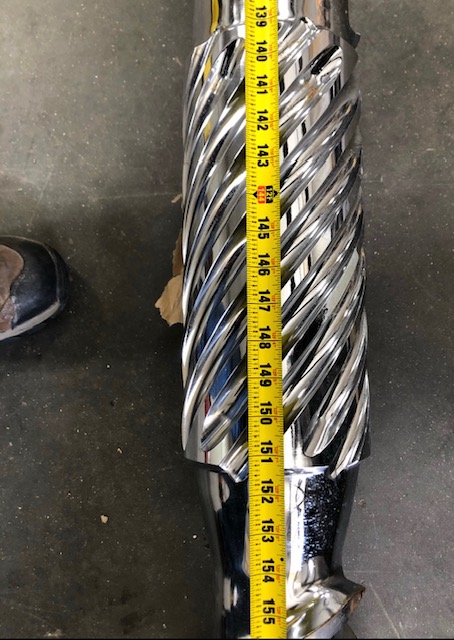
The process of collecting the precise measurements of your feedscrew, barrel, or other associated part.
The following instructions will help you get the information for an accurate Feedscrew quote.
Measuring Fit Dimensions of a Feed Screw (not a complete measurement). We will be measuring the overall dimensions, the shank dimensions, and the key way.
The shank is the space from the end of the bearing to the shank end.
Before getting started with profiling your feed screw to be sent for repair, it is best practice to familiarize yourself with the standard terminology of a typical three-zone general purpose screw. The screw and barrel are major components of production and it is best to measure equipment for wear at least once a year. When a screw is worn, it generates an increase in the melt temperature in the metering section of a screw channel between a normal flight clearance vs. a worn screw with a large flight clearance.
In order to maintain standard production throughput rates, many companies will have the machine operators increase the screw speed. As the screw speed is increase, the shear rate in the screw channel and over the flight lands also increases, causing the melt temperature to increase as well.
This is why it is important to ensure the original screw/barrel clearance is maintained for the best performance of the equipment. A typical total screw to barrel clearance is shown below, per the Society of Plastics Industry guidelines.
Profiling a screw does not require an engineer or specialist, just someone consistent and precise. A sketch similar to the one below can be used to show the dimensions needed to duplicate a screw.
The shank (or drive) of the screw is measured from the "pocket" of the screw to the end of the shank (or drive). The overall shank length will include the "bearing area" and the drive mechanism whether or not it is a keyed drive or spline drive. The outside diameters and lengths of the bearing area and the drive mechanism need to be recorded and inspected for wear, galling or any other damages. Most extrusion screw ends have a deep drilled hole through the core of the screw so that screw cooling can be installed on the screw. This drill size and tap size need to be detailed as well, the thread will typically be National Pipe Threads in the U.S. or British Straight Pipe Threads in other parts of the world.
The shank length is taken from the pocket back to the very end of the shank. If the plan is to duplicate the existing screw, the dimensions taken must be accurate because this is the portion that fits into the drive quill of the gearbox or injection unit. For spline drives, they will usually be either standard, straight-sided splines or conventional, involute splines. For straight-sided splines, the number of splines, width and length is usually all that is needed. For involute splines, the number of teeth on the spline, the outside major diameter of the spline and the length of the spline are the most critical dimensions needed.
Using dial calipers, measure the root diameter of the screw at every turn of the screw over its entire length. Start at the feed section and measure towards the nose end of the screw. The root diameter will measure very close in diameter, turn to turn. It is helpful to mark the root diameter of each turn on the root for easy reference.
Once you determine the root diameter, the channel depth is able to be determined: Subtract the root diameter from the nominal screw outside diameter and divide that by 2.
At the point where the feed section ends and the transition section begins, the root diameter beings to increase. A mark will need to be made on the root of the screw at this instance. Once the end of the feed section has been established, use a tape measure and measure from the end of the shank (or beginning of the pocket) to the mark at the end of the feed. Note this length on your sketch diagram.
Once the feed section length and root diameter has been established, the metering length and channel depth are able to be determined. You can use the same methodology as you just did but in reverse. Starting at the end of the metering section, measure the root diameter of the screw every turn and mark the dimension on the root of the screw. Where the root diameter begins to get smaller, this is where the metering starts and the transition section ends. Using a tape measure, measure the distance from the end of the metering to the mark on the root where the transition section and metering section meet. If there is a two stage screw being profiled, the vent section and the second metering section would be determined in the same manner as the first stage sections were established.
Determining the metering section channel is the same equation as the feed depth: Once you determine the root diameter, the channel depth is able to be determined: Subtract the root diameter from the nominal screw outside diameter and divide that by 2.
Once the feed section and metering length have been established, the length of the transition section can be determined: measure from the pocket to the end of the first metering to verify the length of the first stage. The subtract the length of the feed and metering sections from the length to determine the transition length.
Typically the flight lead is equal to the screw diameter. This is what is referred to as having a "square" lead; ie: a 3.5" screw would have a 3." flight lead. Measuring from the leading edge of one of the flight to the leading edge of the next flight will determine the distance at which the flight travels as it makes one full turn. This is the case with a single-flighted screw.
If you have a double or triple or even quad flighted, the distance the flight travels as it makes one full turn is its lead. In the case of a screw that is double flighted, the distance between the first flight and the next flight is the "pitch." In the case of a 3.5" double flighted screw, the lead could be 3.5" and its pitch 1.75". Barrier type screws require special attention because the distance between flights will not be equal. This is done by design. For the flight width of a screw, the flight width, designated by the letter (e) is typically 10% of the screw diameter. In the case of our 3.5" screw example, the flight width would be .350".
Measuring the screw flight OD is critical and intensive, it is most accurately performed with a micrometer and a parallel bar.