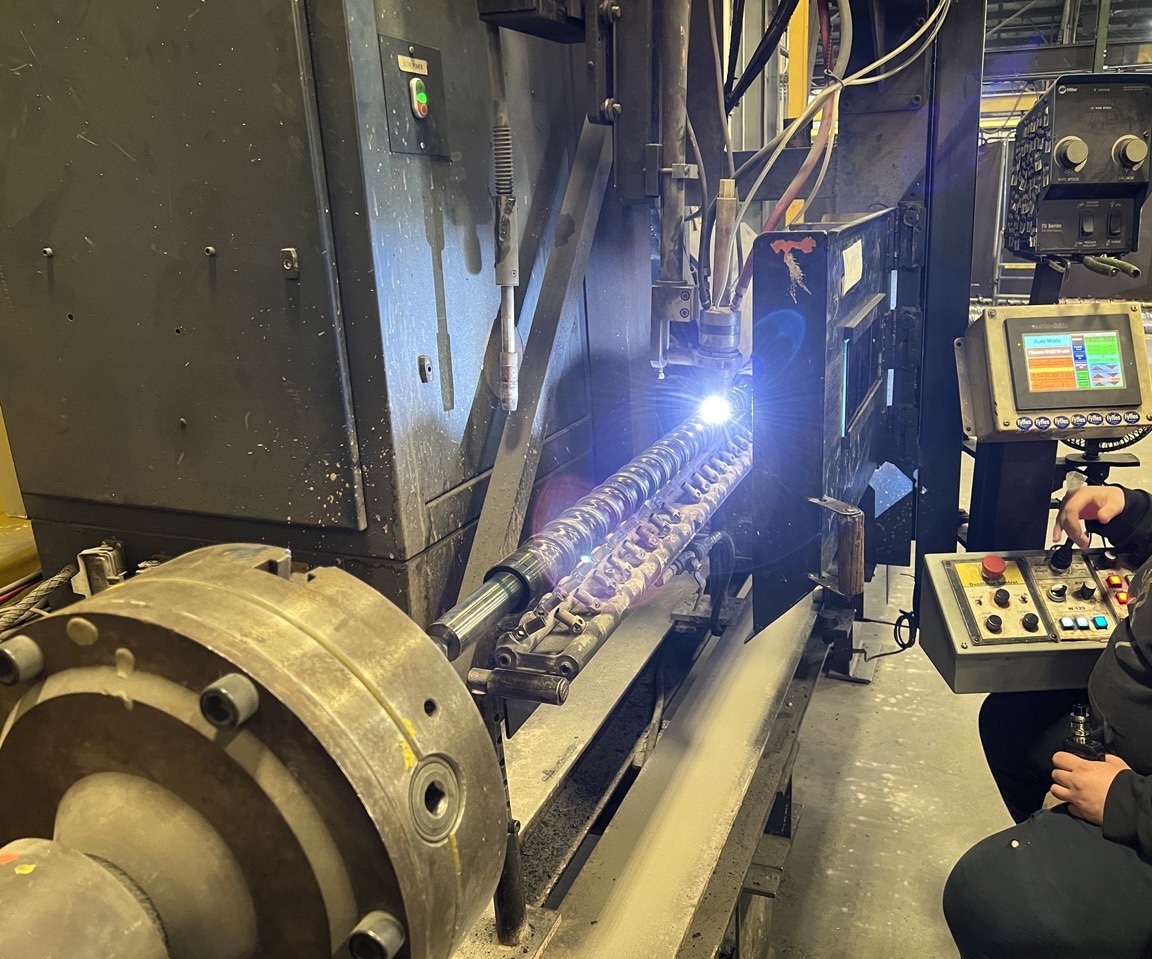
A worn feed-screw decreases production and is detrimental to the quality of your product and increases energy costs. Feed-screw rebuilds are effectively used when you encounter a loss of production directly related to the feed-screw. A multitude of measurements are needed to determine if the feed-screw is a good candidate for a rebuild. The specifications are sent to our Engineering Department and their recommendations are used to create a quote that is prepared and sent to the customer.
Although some situations require the use of a new screw, TIR rebuilds screws to such exact O.E.M. specifications that we warrant all rebuilt screws “same as new”. Screw wear as slight as .030" can reduce production by as much as 55%. We can rebuild screws to such exacting standards that production time is eliminated! Plus, a rebuilt screw from us can save as much as 25-40% over the cost of a new screw. A worn screw decreases production and is detrimental to the quality of your product and increases energy costs.
At TIR, our goal is to provide the most economical way to get the most out of your extrusion or injection molding operation. The feed screw is the prime mover in the extrusion and injection molding process. Careful consideration should be given to the proper screw design for your operation and wear is a key factor that impacts performance. With the same quality standards as our custom screw solutions, we can rebuild your worn screws to save you time and money.
The performance of your plasticating unit is defined by the feed screw’s ability to melt and convey the desired rate and quality of polymer to the die or mold. As the screw flights, channel geometry, and surface treatment wear, performance and quality degrades while energy consumption soars. The overall screw design and material(s) processed has a major impact on the wear-life of the plasticating unit, so it is vital to monitor screw wear and performance, regardless of application. Minor wear will have little effect on the overall performance - as machine parameters can be adjusted to maintain productivity. As the radial clearance gap between the screw and barrel increases, energy costs and cycle times rise while rate and quality plummet. To avoid costly downtime it is important for every company to have a robust maintenance program in place. When screw wear isn't monitored, the overall wear on the screw can become so severe it is no longer economical to rebuild - leaving you with crippling downtime that can ultimately cost more than the components you attempted to salvage.
When we receive your screw for rebuilding, a thorough inspection of the overall condition of your screw as well as the current design is performed. When it is cost effective we can refurbish your screw to like-new condition, re-chrome, nitride, hardface, and even re-cut the existing design to improve performance and wear-life. When a feed screw is rebuilt properly, without narrowing of flight widths, the screw can be rebuilt time and time again - pushing massive savings to your company. With almost 50 years of screw design, manufacturing, and rebuilding experience, we have developed many of the standard feed screw building and rebuilding processes used in the industry today. Trust the experts in screw design, manufacturing, and rebuilding with your production.
Things to consider:
When we receive your damaged screws for rebuilding services, a thorough inspection is performed. Once the extent of the wear, wear patterns, and overall screw design is quantified, we provide you with recommendations for the most cost effective way to get your production up and running. We can manufacture and rebuild screws up to 20" in diameter and sections up to 40 feet in length!
When rebuilding your worn screws, our team applies the highest quality hardface welds. We offer hardfacing options to accommodate any injection molding challenges your team may face.
We re-establish OEM tolerances to all crucial screw dimensions. Once the final OD, channel geometry, drive end, etc. are repaired to spec, your screw is polished to like-new condition. We offer a full range of secondary screw treatments (re-chroming, nitriding, encapsulation, etc.) to improve wear life.
It is of utmost importance to monitor overall screw and barrel wear before your performance and production suffer. Wear can, and has, become so severe that the screw is too costly to repair and you are faced with avoidable downtime. Proper screw and component design partnered with a complete maintenance program help ensure that your company is profitable and competitive in your workflow.
Every company should have a cataloged preventative maintenance program in place to eliminate production loss in downtime. When we build or rebuild screws and components we work closely with you and your team to develop and implement a plan that works. Scheduled annual, biennial or triennial wear evaluation help ensure that you stay ahead of the wear! Rebuilding or replacing screws, barrels, and components before production loss and energy costs skyrocket is important for overall productivity. Just ask and we can help created a tailored screw and barrel rebuilding/replacement program designed with your company's goals and schedule in mind!
Excessive screw and barrel wear comes with rate and quality loss and rising energy consumption. When the radial clearance between the screw flights and barrel wall increase, leakage flow is almost impossible to avoid. In extrusion applications, the operator will typically see a reduction in rate and push it to higher rpms to achieve the desired output. As the material leaks over the screw flights, the material experiences excessive shear. This raises melt temperature, and is only compounded with higher rpm leading to higher energy costs.
In an injection molding environment, screw, barrel, and valve wear can cause a spiderweb of issues. Worn components can cause erratic cushion variation, and even the inability to hold a cushion at all. Worn, and/or damaged components will cause a reduction in plasticizing efficiency, increasing normal recovery time and melt temperatures, naturally increasing overall cycle times. Scrap rates will soar due to potential streaking, burns, and non-uniform parts due to poor melt quality and degradation. Instability in the molding process and increased melt temperature caused from excessive wear will increase cycle times, energy consumption, and waste. Injection screw assembly and barrel wear all leads to wasted time and money!
Give us a call at 1-800-922-7735 and we can work with you on solutions that will meet your needs. TIR can design, rebuild and manufacture a feedscrew from 19mm to 20in diameter and up to 40' in length specific to your process and manufacturing goals.